Automotive Injection Molding: Revolutionizing the Metal Fabrication Industry
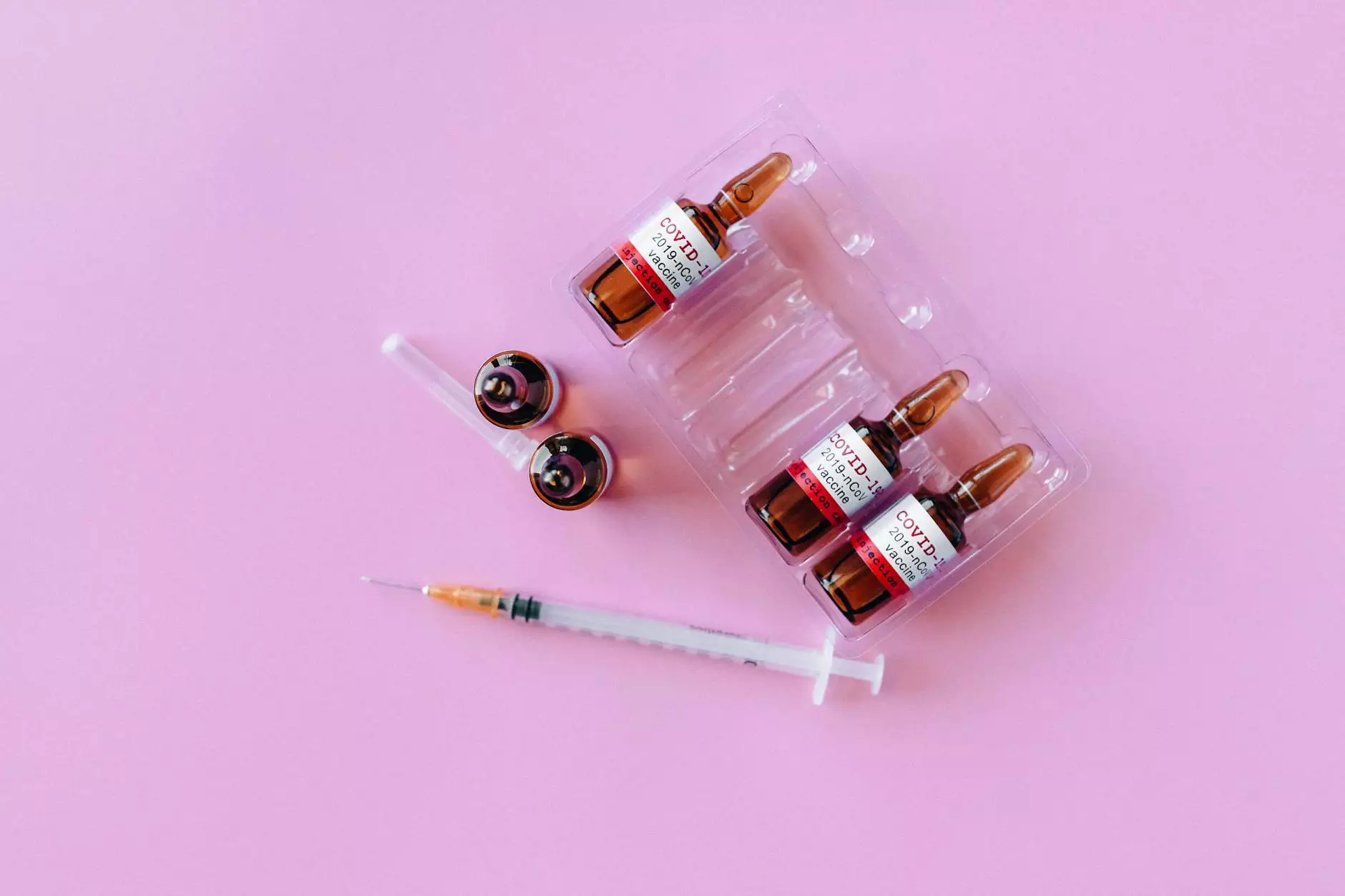
In the fast-paced world of automotive manufacturing, automotive injection molding has emerged as a game-changing process. This technique not only allows for the production of high-quality plastic components but also plays a crucial role in reducing costs, improving efficiency, and ensuring product longevity. In this comprehensive article, we delve into the intricacies of automotive injection molding, its applications, benefits, and how it significantly impacts the operations of metal fabricators.
Understanding Automotive Injection Molding
Automotive injection molding is a manufacturing process where molten plastic is injected into precision-engineered molds to create various automotive parts and components. This method is particularly advantageous in the automotive sector due to its ability to produce complex shapes and designs with high precision and speed.
The process starts with raw plastic materials that are heated until they become viscous. This material is then injected into a mold under high pressure, filling every cavity and detail of the design. Once cooled, the mold is opened, and the finished component is ejected, ready for assembly into vehicles.
The Importance of Injection Molding in the Automotive Industry
- Cost Efficiency: By utilizing automated processes, manufacturers reduce labor costs and improve production times.
- Material Versatility: Various plastics can be used, including thermoplastics and thermosetting, allowing for tailored products.
- High Precision: Injection molding can achieve tolerances as tight as ±0.005 inches, ensuring that components fit together perfectly.
- Minimized Waste: The process produces minimal waste compared to traditional manufacturing methods, promoting a more sustainable approach.
Applications of Automotive Injection Molding
The use of automotive injection molding spans numerous applications, reflecting the versatility of this manufacturing technique. Here are some common applications:
Interior Components
From dashboard panels to door trims, interior components greatly benefit from injection molding. The ability to add intricate textures and colors enhances the aesthetic appeal of the vehicle, while ensuring parts are durable and resistant to wear.
Exterior Components
Exterior parts such as bumpers, fenders, and light housings are often produced using injection molding. The process enables manufacturers to create lightweight yet sturdy components that can withstand the rigors of the road.
Under-the-Hood Parts
Injection molding is also used for various under-the-hood applications, including air intake manifolds and protective covers. These components require materials that can handle high temperatures and harsh environments, which molded plastics provide.
Advantages of Automotive Injection Molding
There are several advantages to using automotive injection molding over other manufacturing techniques, which we will explore in detail:
1. Enhanced Production Speed
The automation of the injection molding process leads to significantly reduced cycle times. Manufacturers can produce large volumes of parts in a fraction of the time compared to traditional methods, allowing them to meet the increasing demands of the automotive market.
2. Complex Geometries
Injection molding allows for the creation of complex designs that would be challenging or impossible to achieve with other manufacturing methods. This flexibility enables automotive designers to innovate freely without being constrained by manufacturing limitations.
3. Consistency and Quality Control
The precision of the injection molding process results in high-quality parts that are consistent in dimension and performance. This consistency is crucial in automotive manufacturing, where the reliability and safety of every component are paramount.
4. Reduction in Material Costs
With advanced material technologies, manufacturers can select plastics that not only reduce weight but also enhance performance. The use of recycled materials in the injection molding process also promotes sustainability while lowering costs.
Challenges in Automotive Injection Molding
Despite its advantages, the automotive injection molding process presents several challenges that manufacturers must navigate:
1. Initial Tooling Costs
The creation of molds for injection molding can be expensive and time-consuming. However, this cost is typically offset by the high volume of parts produced and the associated savings in labor and material costs.
2. Design Limitations
While injection molding allows for complex designs, there are still constraints to consider, such as the draft angles required for mold release. Designers must collaborate closely with engineers to optimize part designs for manufacturability.
3. Production Changeover Time
Switching between different product designs can require significant setup time. However, with the right planning and scheduling, manufacturers can streamline this process to minimize downtime.
The Future of Automotive Injection Molding
The future of automotive injection molding looks promising, driven by technological advancements and the growing demand for efficient manufacturing processes. Integrating smart technologies, such as automation and IoT, will enhance the efficiency and precision of injection molding.
Innovations in Material Technology
New materials, including bio-based and recycled plastics, are emerging, pushing the boundaries of what is possible in injection molding. These innovations not only enhance performance but also align with growing environmental concerns.
Emphasis on Sustainability
As the automotive industry moves towards sustainability, automotive injection molding will play a vital role in manufacturing lighter, more efficient vehicles. The ability to efficiently utilize resources and minimize waste will be crucial in meeting regulatory requirements and consumer expectations.
Conclusion: Embracing the Change in Metal Fabrication
The rise of automotive injection molding represents a significant shift in the way metal fabricators and automotive manufacturers approach production. As this technology evolves, it promises to deliver even greater efficiency, flexibility, and sustainability. By adopting and integrating these advanced techniques, companies like those found at deepmould.net can position themselves at the forefront of innovation in the automotive industry.
In summary, as the automotive sector continues to grow and adapt, embracing the advancements offered by automotive injection molding is essential for any metal fabricator aiming to stay competitive and meet the challenges of tomorrow.