Understanding Precision Injection Molding Manufacturers
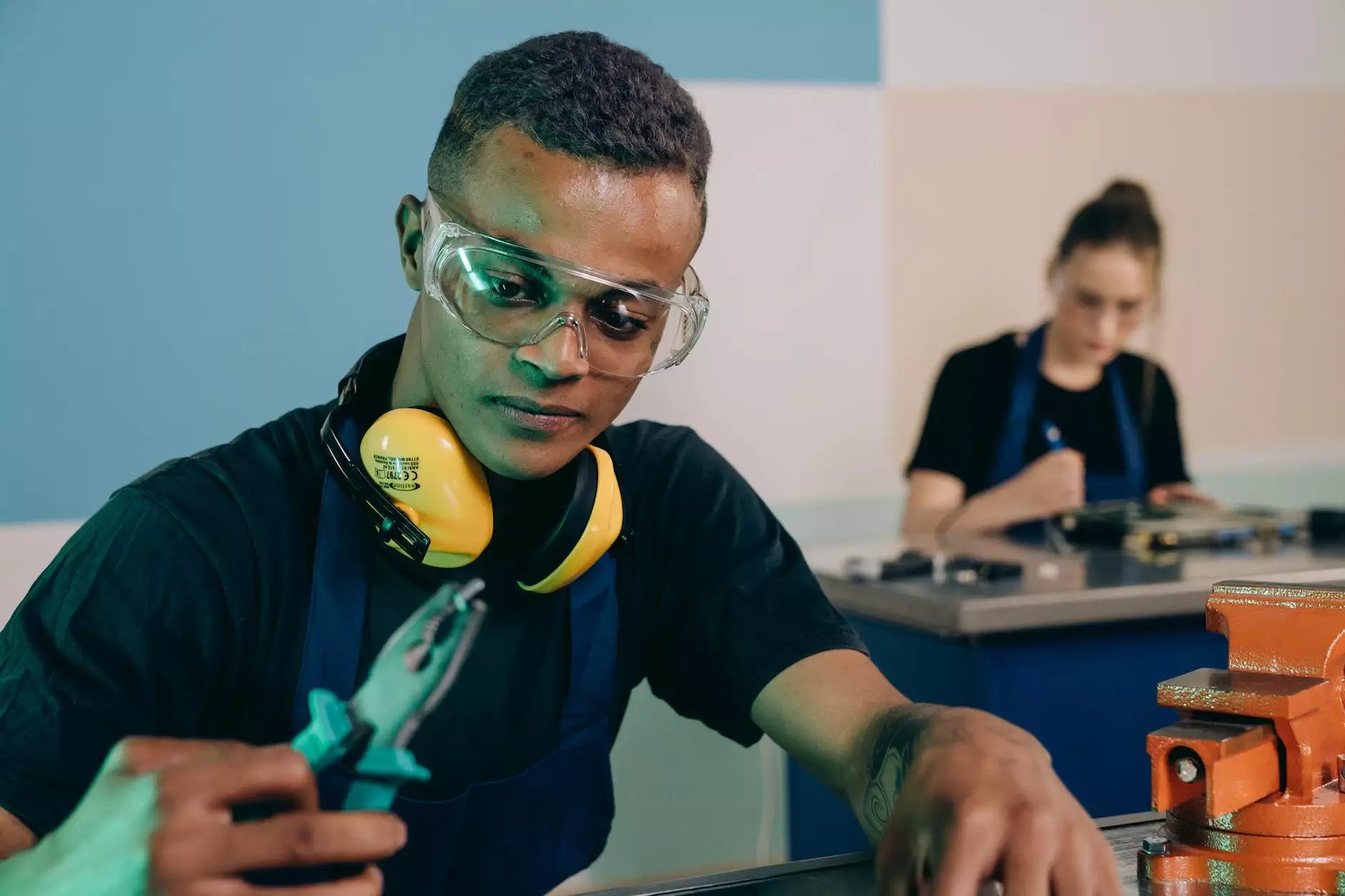
Precision injection molding manufacturers play a crucial role in the production of high-quality plastic components for various industries. In today’s competitive market, leveraging advanced manufacturing techniques is essential for businesses looking to gain a competitive edge. This article delves into the intricacies of precision injection molding, its benefits, and how it serves as a backbone of modern manufacturing.
What is Precision Injection Molding?
Precision injection molding is a manufacturing process used to create complex parts and components from thermoplastic materials. It involves injecting molten plastic into a mold, where it cools and solidifies to form the final product. The key features of this process include:
- High Accuracy: The precision of the molding process ensures that components are produced with tight tolerances and minimal variation.
- Repeatability: Once the mold is designed, the process can be repeated countless times, yielding identical products.
- Efficiency: This method reduces waste and shortens production time, making it an economical choice for mass production.
Why Choose a Precision Injection Molding Manufacturer?
Businesses must choose the right precision injection molding manufacturer to ensure their products meet the highest quality standards. Here are some compelling reasons to partner with a top-notch manufacturer:
1. Expertise and Experience
Leading manufacturers bring a wealth of industry knowledge and experience. Their expertise in handling various materials and complex designs ensures that your parts are both functional and aesthetically pleasing.
2. Advanced Technology
The best manufacturers invest in state-of-the-art equipment to enhance production capabilities. From computer-aided design (CAD) to precision robotics, these technologies allow for intricate designs that were once impossible to achieve.
3. Quality Assurance
With rigorous quality control processes in place, precision injection molding manufacturers ensure that every component meets industry specifications. This commitment to quality minimizes defects and ensures customer satisfaction.
4. Customization Options
Every business has unique requirements. Leading manufacturers offer customization options to meet specific project needs, whether it's size, shape, or material. This flexibility can greatly enhance the functionality of your products.
The Process of Precision Injection Molding
The manufacturing process involves several steps, each critical to achieving the desired outcome:
1. Design and Prototyping
The journey begins with an idea. Through the use of CAD software, manufacturers can design the component and create prototypes. Prototyping is essential for identifying any design flaws before mass production begins.
2. Mold Creation
After finalizing the design, the next step is creating the mold. Molds are typically constructed from durable materials such as steel or aluminum to withstand the injection process. The precision of the mold directly influences the quality of the final product.
3. Injection Process
Once the mold is ready, the raw plastic material is heated until it becomes molten. The molten plastic is then injected into the mold under high pressure. This process allows the material to fill every intricate detail of the mold.
4. Cooling and Ejection
After filling the mold, the plastic is allowed to cool and solidify. Once sufficiently cooled, the mold opens, and the finished product is ejected. This stage must be handled carefully to prevent any damage to the parts.
5. Finishing Touches
Many manufacturers offer secondary processes such as trimming, painting, or assembling, ensuring that the product is ready for distribution. This holistic approach enhances the product's overall quality and appeal.
Industries Benefiting from Precision Injection Molding
Precision injection molding serves various industries, including:
- Automotive: Components like dashboards, lights, and panels are often produced using this method due to the precision required in automotive applications.
- Medical: Medical devices and components require high standards of hygiene and reliability, making injection molding an ideal choice.
- Consumer Electronics: From smartphone casings to intricate parts, precision molding is crucial for maintaining functionality and aesthetic appeal.
- Packaging: Innovative packaging solutions often leverage injection molding for custom designs and high durability.
Benefits of Precision Injection Molding for Businesses
Investing in precision injection molding has several advantages for businesses:
1. Cost-Effectiveness
While the initial investment in molds can be significant, the overall cost per unit decreases with higher production volumes. Precision injection molding manufacturers help businesses save money in the long run.
2. Material Efficiency
This process is known for its minimal waste generation as excess plastic can often be reused. This not only reduces costs but also contributes to more sustainable manufacturing practices.
3. Scalability
As businesses grow, their production needs may change. Precision injection molding allows for easy adjustments in production scale, accommodating increasing demands without a drastic shift in production processes.
4. Environmental Impact
Modern precision injection molding manufacturers are adopting eco-friendly practices, utilizing recyclable materials and reducing emissions, thereby aligning with global sustainability efforts.
Choosing the Right Precision Injection Molding Manufacturer
Finding the right manufacturing partner is vital for success. Consider the following factors:
1. Reputation and Experience
Research the manufacturer's track record in the industry. Look for recommendations, customer reviews, and case studies.
2. Capabilities
Ensure that the manufacturer has the necessary technology and expertise to handle your specific requirements, whether they involve complex geometries or specialized materials.
3. Communication
Effective communication is essential for a smooth production process. Choose a manufacturer that prioritizes transparency and keeps clients informed at every stage.
4. Post-Production Support
Consider manufacturers that offer comprehensive support after production, including assembly, packaging, and shipping services.
The Future of Precision Injection Molding
The landscape of precision injection molding is continually evolving. With advancements in technology such as smart manufacturing and automation, manufacturers are poised to deliver even greater efficiency and quality. Emerging trends include:
- AI and Machine Learning: These technologies facilitate predictive maintenance, ensuring optimal performance of equipment and reducing downtime.
- 3D Printing Integration: By combining traditional injection molding with 3D printing, manufacturers can create more complex designs and streamline production.
- Sustainability Initiatives: Continuous efforts to reduce environmental impact through the use of biodegradable materials and energy-efficient machinery.
Conclusion
In conclusion, partnering with a reliable precision injection molding manufacturer is a game-changer for businesses looking to innovate and improve their product offerings. By understanding the advantages and processes involved in precision injection molding, companies can make informed decisions that lead to greater efficiency, lower costs, and superior product quality. As the industry evolves, those who stay ahead of the curve will reap the benefits of this powerful manufacturing process.