Unleashing the Power of Injection Molding Shops for Your Business
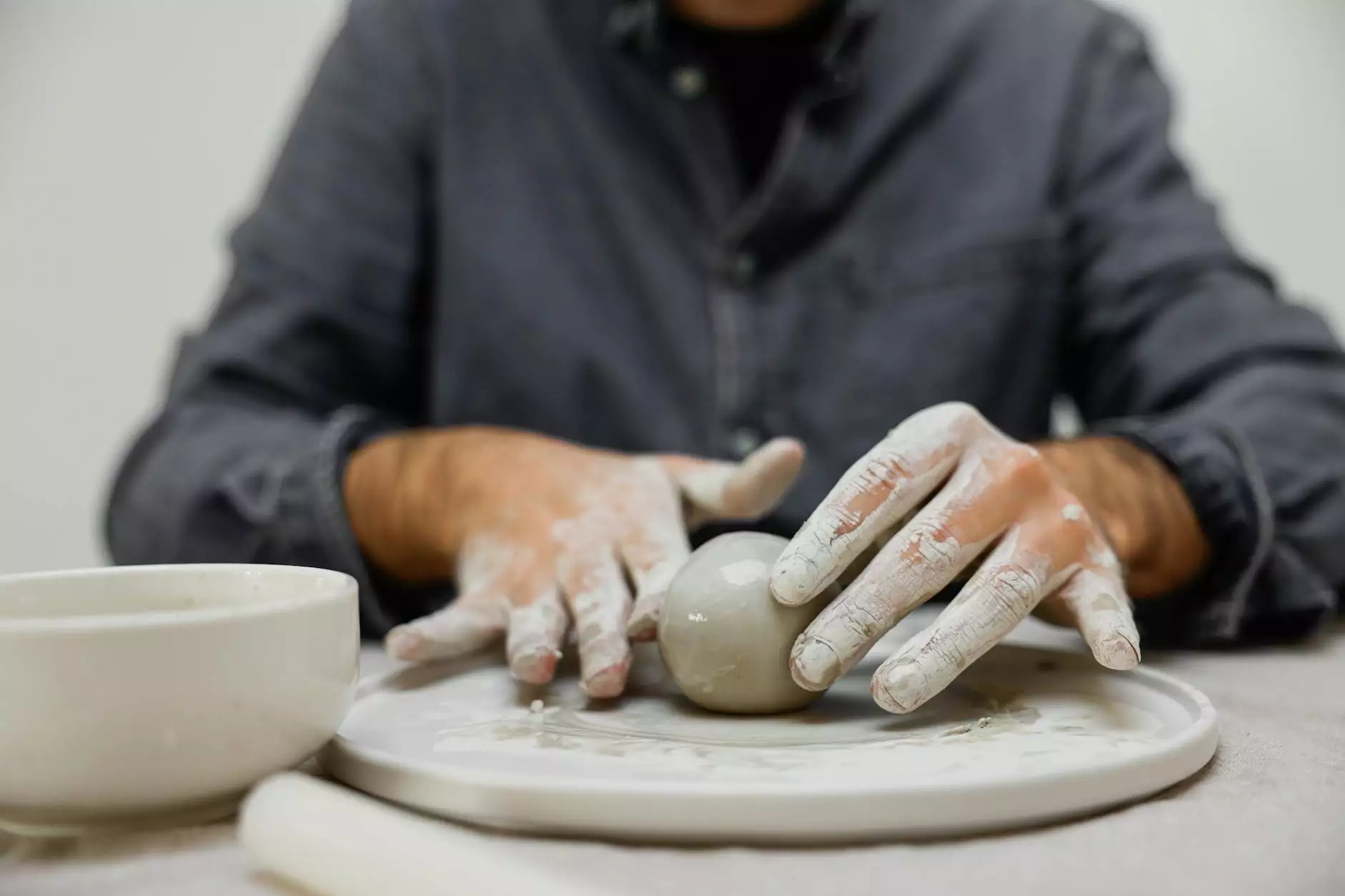
In today's fast-paced manufacturing industry, the importance of efficiency and precision cannot be overstated. Injection molding shops play a crucial role in this realm, providing businesses with the tools and capabilities needed to develop high-quality plastic products. In this article, we will explore the myriad benefits of collaborating with professional injection molding shops, delve into the intricacies of the injection molding process, and highlight how your business can thrive in an increasingly competitive marketplace.
The Basics of Injection Molding
Injection molding is a manufacturing process in which molten plastic is injected into a mold to create a desired shape. This method is highly efficient and allows for the production of complex geometries with excellent repeatability—an essential factor for high-volume production runs.
Key Components of the Injection Molding Process
- Mold Design: The creation of an effective mold is critical. It requires a deep understanding of the end product, materials, and manufacturing capabilities.
- Material Selection: Choosing the right type of plastic is essential as it affects the durability, flexibility, and overall quality of the final product.
- Injection: During this phase, the plastic pellets are heated until they melt and are then injected into the mold under high pressure.
- Cooling: The material is allowed to cool and solidify in the mold, which is a vital step to ensure precision.
- Finishing: Once the molded part is ejected, additional processes like trimming and surface finishing may be necessary to achieve the desired quality.
Why Choose Professional Injection Molding Shops?
When it comes to finding the right partner for your injection molding needs, choosing a professional injection molding shop can be transformative. Here are several reasons why:
1. Expertise and Experience
Injection molding shops like Hanking Mould possess extensive experience in the industry, ensuring that every project benefits from their wealth of knowledge. Their team of skilled engineers and technicians can guide you through every step of the process, from design to production.
2. Advanced Technology
Modern injection molding shops utilize cutting-edge technology, including computer-aided design (CAD) and computer-aided manufacturing (CAM) systems. This technology allows for precise mold creation and helps ensure high-quality outputs.
3. Cost Efficiency
By outsourcing your injection molding needs to a specialized shop, you can reduce overhead costs associated with in-house production. Injection molding shops can produce high volumes of parts at a lower cost than traditional manufacturing methods, making them an economically viable option for businesses of all sizes.
4. Scalability
Injection molding is particularly beneficial for companies looking to scale their production. Whether you're running a small batch or planning for mass production, injection molding shops can accommodate your changing needs without sacrificing quality or efficiency.
Industries Served by Injection Molding Shops
Injection molding shops serve a diverse array of industries, including:
- Automotive: Manufacturing components such as dashboards, bumpers, and interior fittings.
- Consumer Goods: Producing everyday items like kitchenware, toys, and personal care products.
- Medical Devices: Creating specialized equipment and components that require high precision and compliance with medical standards.
- Electronics: Fabricating casings and components for various electronic devices.
- Packaging: Designing and producing containers, lids, and other packaging solutions.
Insights into the Plastic Mold Maker Role
Within the injection molding shops, the role of a plastic mold maker is paramount. They are responsible for creating the molds used in the injection molding process, and their expertise directly impacts the quality of the final product. Here are some vital aspects to consider:
1. Precision Engineering
A plastic mold maker employs advanced machining techniques and tools to ensure that molds are crafted with utmost precision. This precision is critical as any deviation can affect the quality and functionality of the final product.
2. Material Knowledge
Understanding the properties of various materials is essential for mold makers. Different plastics have unique characteristics that affect their molding behavior, shrink rates, and thermal properties. A knowledgeable plastic mold maker can help select the most appropriate materials for a given application.
3. Problem-Solving Skills
Challenges often arise during the mold-making process. A skilled plastic mold maker must possess strong problem-solving skills to address issues on the fly, ensuring that production remains on schedule and services are delivered without delay.
Future Trends in Injection Molding
The injection molding industry is evolving, thanks to advancements in technology and changing market demands. Here are some trends to watch:
1. Sustainability Practices
There is a growing emphasis on sustainability within the manufacturing sector. Injection molding shops are increasingly adopting eco-friendly materials, such as those derived from renewable resources, as well as implementing more efficient production processes to minimize waste.
2. Industry 4.0 Integration
The integration of IoT and smart manufacturing technologies is transforming injection molding. Real-time data collection and monitoring enable injection molding shops to optimize processes, reduce downtime, and enhance product quality.
3. Additive Manufacturing Collaboration
3D printing is increasingly being used in conjunction with injection molding, particularly for prototyping and creating complex mold geometries. This collaboration allows for greater flexibility in design and faster development times.
Choosing the Right Injection Molding Shop
To maximize the benefits of working with injection molding shops, it is essential to choose the right partner. Here are some tips for making the best choice:
1. Evaluate Their Portfolio
Review previous projects to gauge the quality of their work. Look for examples relevant to your industry to ensure they have the necessary expertise.
2. Assess Their Technology
Ensure that the shop uses modern equipment and techniques. Advanced technology is a good indicator of their capability to produce high-quality products.
3. Request Customer References
Speaking with past clients can provide valuable insights into the shop's reliability, communication, and overall performance.
4. Discuss Lead Times and Costs
Understand their pricing structure and lead times to ensure they align with your project's budget and deadlines.
Conclusion
Injection molding shops provide an invaluable service in the world of manufacturing. By leveraging advanced technologies, expertise, and cost efficiencies, businesses can produce high-quality plastic components that meet the demands of today's market. Whether you are a startup looking to launch a new product or an established enterprise seeking to enhance your manufacturing processes, collaborating with a reputable injection molding shop like Hanking Mould can set your business on the path to success.
Final Thoughts
The future of manufacturing lies in innovation and efficiency, and injection molding shops are at the forefront of this evolution. Embrace the potential of injection molding today and watch your business transform and thrive in an ever-competitive landscape.