The Comprehensive Guide to Plastic Molding Injection for Metal Fabricators
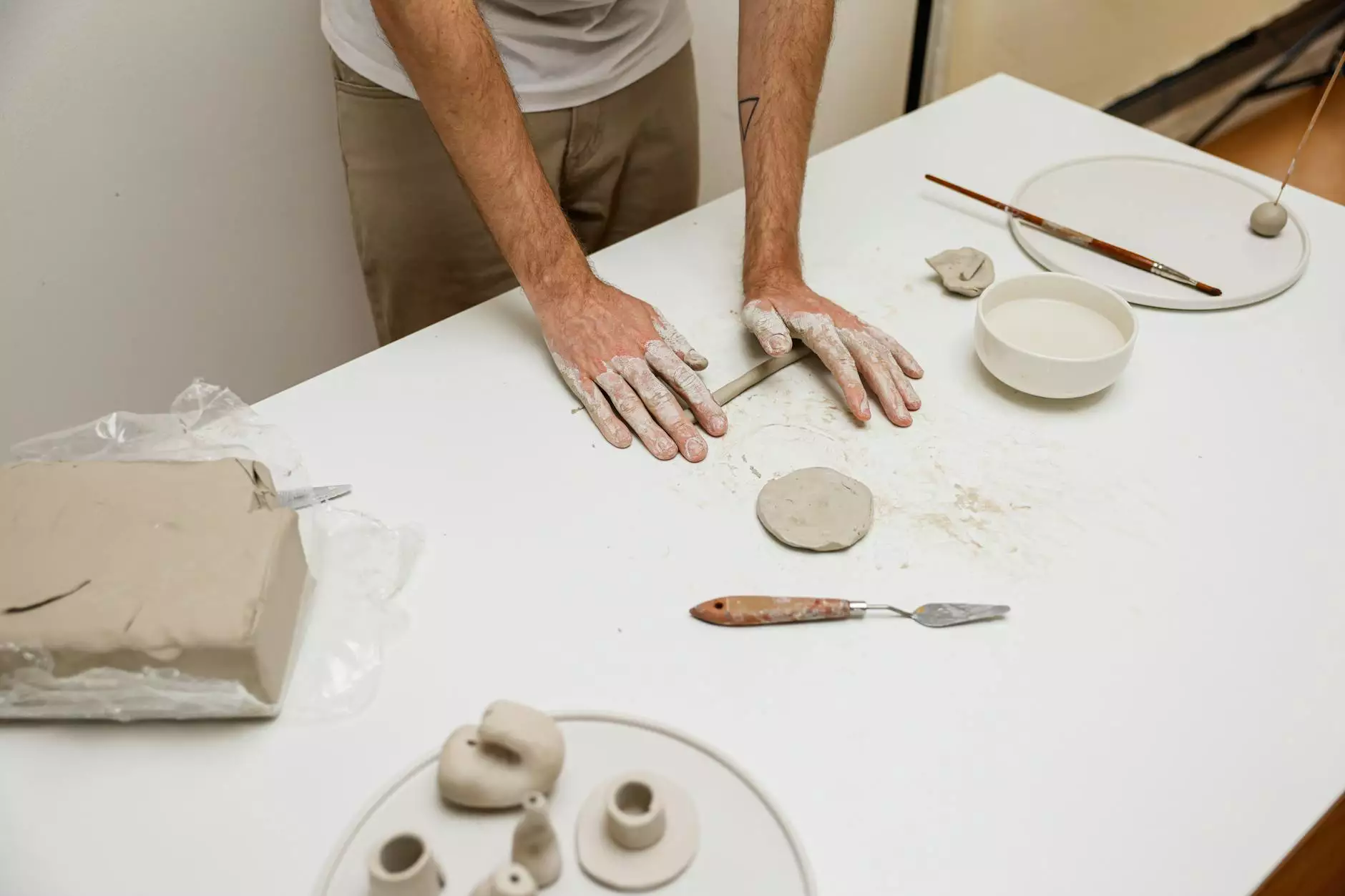
In the ever-evolving landscape of manufacturing, plastic molding injection stands out as a pivotal technique, particularly in the domain of metal fabricators. This article delves into the nuances of plastic molding injection, discussing its significance, advantages, and practical applications in the fabrication industry.
Understanding Plastic Molding Injection
Plastic molding injection is a manufacturing process used for creating parts by injecting molten material into a mold. This method is widely employed due to its efficiency in producing complex shapes with high precision. The process begins when plastic granules are fed into a heated barrel, where they are melted into a liquid state. The liquid plastic is then injected into a mold under high pressure, allowing it to take the shape of the desired part once cooled and solidified.
The Process of Plastic Molding Injection
- Material Preparation: The raw plastic material is prepared in pellet form and fed into the injection molding machine.
- Heating: The pellets are heated until they become a molten liquid, ensuring they can flow easily into the mold.
- Injection: The molten plastic is injected into the mold cavity at high pressure.
- Cooling: The mold is cooled to solidify the plastic, allowing it to maintain the shape of the mold.
- Demolding: Once cooled, the mold opens to release the finished part.
- Finishing: Additional processes such as trimming, painting, or assembly may be applied.
Significance of Plastic Molding Injection in Metal Fabrication
For metal fabricators, incorporating plastic molding injection into their manufacturing processes offers several advantages. The primary benefits are detailed below:
1. Cost-Effectiveness
One of the most compelling reasons to employ plastic molding injection is its cost-effectiveness. The process minimizes material wastage and reduces labor costs due to automated machinery. This efficiency leads to a lower overall production cost, making it attractive for manufacturers aiming to maximize profits.
2. High Precision and Quality
The precision of the injection molding process ensures that parts are manufactured to exact specifications with minimal tolerances. This quality enhancement is crucial for metal fabricators who require integration of plastic components in their products for durability and functionality.
3. Scalability
Plastic molding injection allows for the production of large quantities of parts with consistent quality. This scalability is invaluable for businesses looking to meet high demands without compromising on standards.
4. Versatility in Design
The design versatility afforded by injection molding enables fabricators to create intricate components that may otherwise be difficult or impossible to manufacture using traditional methods. From lightweight structures to complex geometries, plastic molding injection can cater to various design requirements.
5. Material Options
Injection molding supports a wide range of materials including thermoplastics and thermosetting plastics. This material versatility empowers metal fabricators to use the most suitable material for each application, optimizing product performance.
Application of Plastic Molding Injection in Metal Fabrication
The applications of plastic molding injection in the metal fabrication industry are diverse and expanding. Here are some of the most notable uses:
1. Automotive Industry
In the automotive sector, plastic parts are extensively used for interior and exterior components. The durability, lightweight, and design flexibility of molded plastics complement metal parts, enhancing vehicle performance and aesthetics.
2. Consumer Electronics
With the growing demand for electronic devices, plastic molding injection is crucial for fabricating components such as casings, connectors, and intricate internal parts. This method allows for the integration of functionalities into compact designs, meeting consumer demands for both innovation and performance.
3. Medical Devices
The medical industry benefits greatly from plastic molding injection due to the need for precision and compliance with strict medical regulations. Many devices, including surgical tools and housings for sensitive electronic equipment, are produced using this method to ensure reliability and hygiene.
4. Retail and Packaging
Plastic molding has revolutionized product packaging, from containers and bottles to elaborate blister packs. The ability to produce lightweight and durable packaging solutions helps brands in retail streamline their logistics and reduce environmental impact.
Challenges in Plastic Molding Injection
While plastic molding injection offers numerous benefits, there are challenges that metal fabricators must consider when incorporating this technology into their production lines.
1. Initial Setup Costs
The initial costs associated with purchasing injection molding machines and creating molds can be significant. However, the long-term savings achieved through efficient production processes often justify these initial investments.
2. Complexity of the Process
The injection molding process itself can be complex, requiring skilled operators who understand the intricacies of the machinery and material properties. Continuous training and development for personnel are essential to maintain production efficacy.
3. Material Limitations
While plastic molding offers diverse material choices, not all plastics are suitable for every application. Fabricators must assess material properties against performance requirements to avoid compromising quality.
Future Trends in Plastic Molding Injection
As technology advances, the realm of plastic molding injection is poised for transformation. Here are some anticipated trends that could shape the future:
1. Sustainability Advances
The push for sustainable manufacturing practices has led to the development of biodegradable plastics and recycled materials. Future injection molding processes will likely incorporate these materials, reducing environmental impact.
2. Automation and Industry 4.0
Automation in plastic molding processes is expected to rise significantly, enhancing efficiency and quality control while reducing human error. The integration of IoT and data analytics will optimize production lines, ensuring timely maintenance and operational effectiveness.
3. Customization and Personalization
Consumers increasingly demand customized products. Advances in plastic molding injection can enable shorter production runs for personalized items without sacrificing quality or increasing costs. This personalization trend denotes a shift in production strategies.
Conclusion
In conclusion, plastic molding injection offers an array of benefits and opportunities for metal fabricators. By understanding the process, applications, and implications of this technique, businesses can harness its potential to enhance their manufacturing capabilities. As the industry continues to evolve, staying informed about the latest trends and advancements will be crucial for staying competitive. For more insights and solutions in the world of plastic molding injection, visit deepmould.net today.