Precision Plastic Molding: The Backbone of Modern Manufacturing
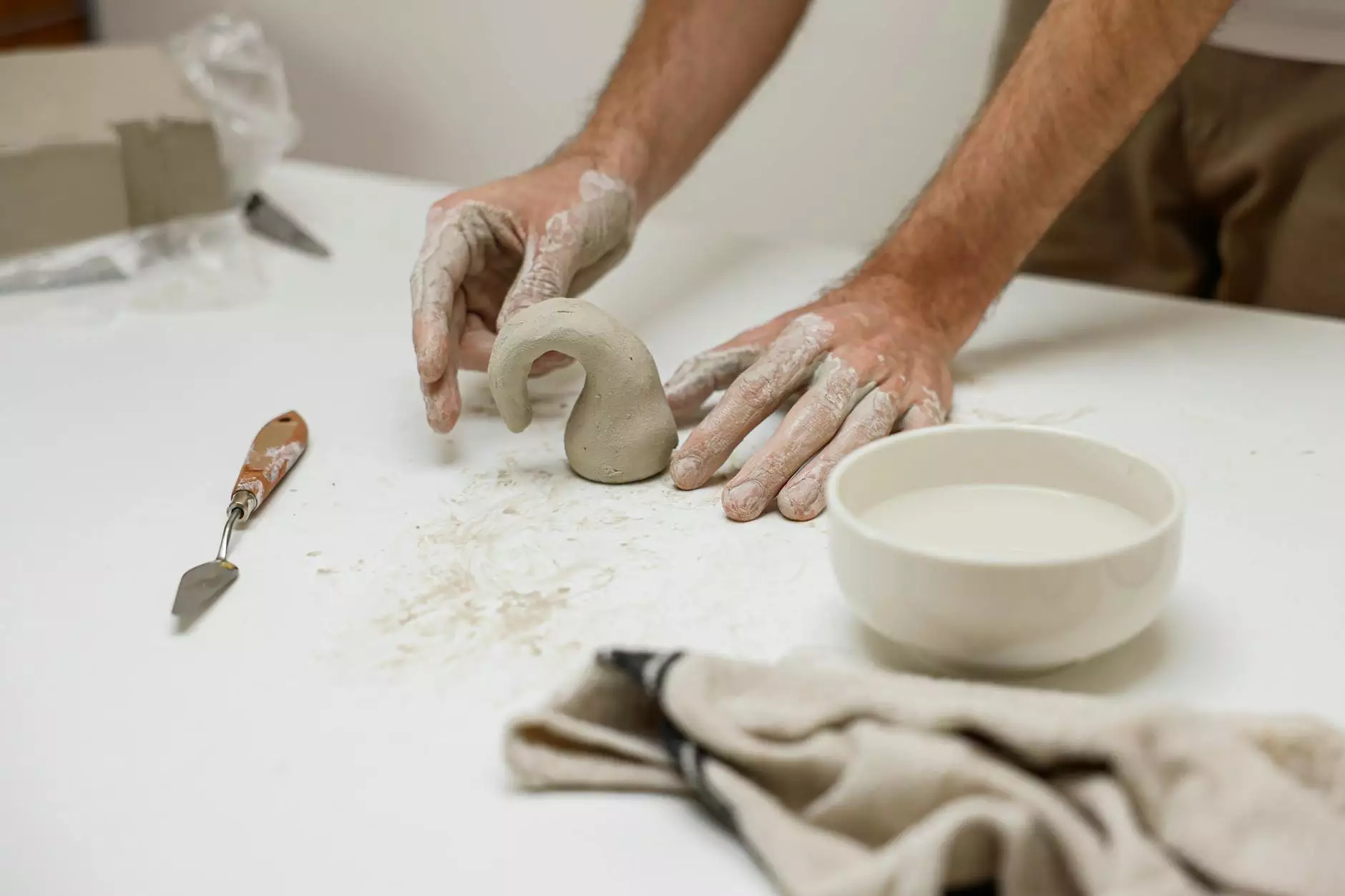
Introduction to Precision Plastic Molding
Precision plastic molding serves as a cornerstone for countless industries today. The method involves intricate processes to create high-precision plastic parts that meet the exacting standards of various applications. This comprehensive guide delves deep into the methodologies, benefits, and future of precision plastic molding.
The Process of Precision Plastic Molding
The process of precision plastic molding is both an art and a science, involving several key steps to ensure quality and precision:
- Material Selection: Choosing the appropriate plastic material is crucial. Common materials include ABS, polycarbonate, and polypropylene, each offering unique properties suited for different applications.
- Mold Design: Engineers create detailed designs that include specifications for dimensions, surface finish, and weight. The precision of the mold is vital for the accuracy of the final product.
- Injection Molding: The selected plastic is heated until it melts, and then injected into a mold under high pressure. This step requires precise control to avoid defects.
- Cooling and Ejection: Once the mold is filled, it is cooled to solidify the plastic. After reaching the appropriate temperature, the molded part is ejected from the mold.
- Finishing and Quality Control: The final step involves inspecting the parts for dimensions, surface quality, and any potential defects. Techniques such as ultrasonic testing and visual inspections ensure the highest quality standards are met.
Advantages of Precision Plastic Molding
Utilizing precision plastic molding offers numerous advantages that enhance manufacturing efficiency and product quality:
- High Tolerance Levels: This method produces components with extremely tight tolerances, crucial for industries like aerospace, automotive, and medical devices.
- Cost Efficiency: Once the initial mold is created, producing large volumes of parts can significantly reduce costs per unit compared to other manufacturing methods.
- Complex Geometries: Precision molding can create complex designs that would be difficult or impossible to achieve with traditional manufacturing techniques.
- Material Versatility: A wide variety of thermoplastics can be molded, allowing manufacturers to choose materials that best suit their specific technical requirements.
- Scalability: Whether producing small, precise components or large batches of parts, this method can scale efficiently to meet production demands.
Applications of Precision Plastic Molding
Precision plastic molding is employed across a vast array of industries:
Aerospace and Defense
In aerospace, lightweight and durable components are essential for aircraft efficiency. Precision molding is used to create parts that meet stringent safety and performance standards.
Healthcare and Medical
Medical devices often require precise components that are both reliable and hygienic. Precision plastic molding facilitates the production of disposable items, surgical instruments, and complex drug delivery systems.
Automotive
The automotive industry benefits from precision molding through the creation of intricate parts used in vehicle interiors, electronics, and under-the-hood applications, contributing to both performance and safety.
Consumer Products
Many of the everyday products we use—from household items to electronics—rely on precision plastic molding for their intricate designs and functionality, ensuring they meet user demands.
The Future of Precision Plastic Molding
As technology evolves, so does the process of precision plastic molding. Some trends shaping the future include:
Automation and Robotics
Integrating robotics into the molding process enhances efficiency and reduces human error. Automated systems can take over repetitive tasks while maintaining high precision.
3D Printing and Hybrid Manufacturing
The combination of 3D printing with traditional molding techniques is revolutionizing prototyping and production, allowing companies to rapidly develop and test new designs.
Sustainability Initiatives
With increasing environmental concerns, manufacturers are exploring biodegradable materials and recycling processes that reduce waste and carbon footprints throughout the precision plastic molding lifecycle.
Smart Manufacturing
The advent of Industry 4.0 introduces smart technologies, enabling real-time monitoring and optimization of the molding process to improve quality and reduce lead times significantly.
Choosing the Right Partner for Precision Plastic Molding
Working with an experienced manufacturer is critical for achieving desired outcomes in precision plastic molding. When selecting a partner, consider the following:
- Experience and Expertise: Choose a company with a proven track record in your particular industry.
- Technology and Equipment: Ensure they utilize advanced machinery and up-to-date technology to deliver high-quality products.
- Quality Assurance Processes: Inquire about their quality control measures and certifications to ensure rigorous standards.
- Customer Support: A responsive and knowledgeable support team can significantly enhance your experience and address any issues that arise during production.
Conclusion
In conclusion, precision plastic molding is not just a manufacturing method; it is an essential element of modern production across numerous industries. Its advantages in efficiency, cost, and quality make it a preferred choice for businesses aiming to innovate and lead in their respective fields. By staying informed of technological advancements and industry trends, companies can harness the full potential of precision plastic molding to thrive in a competitive landscape.