Understanding GRP Manufacturers: Their Role and Impact on Industries
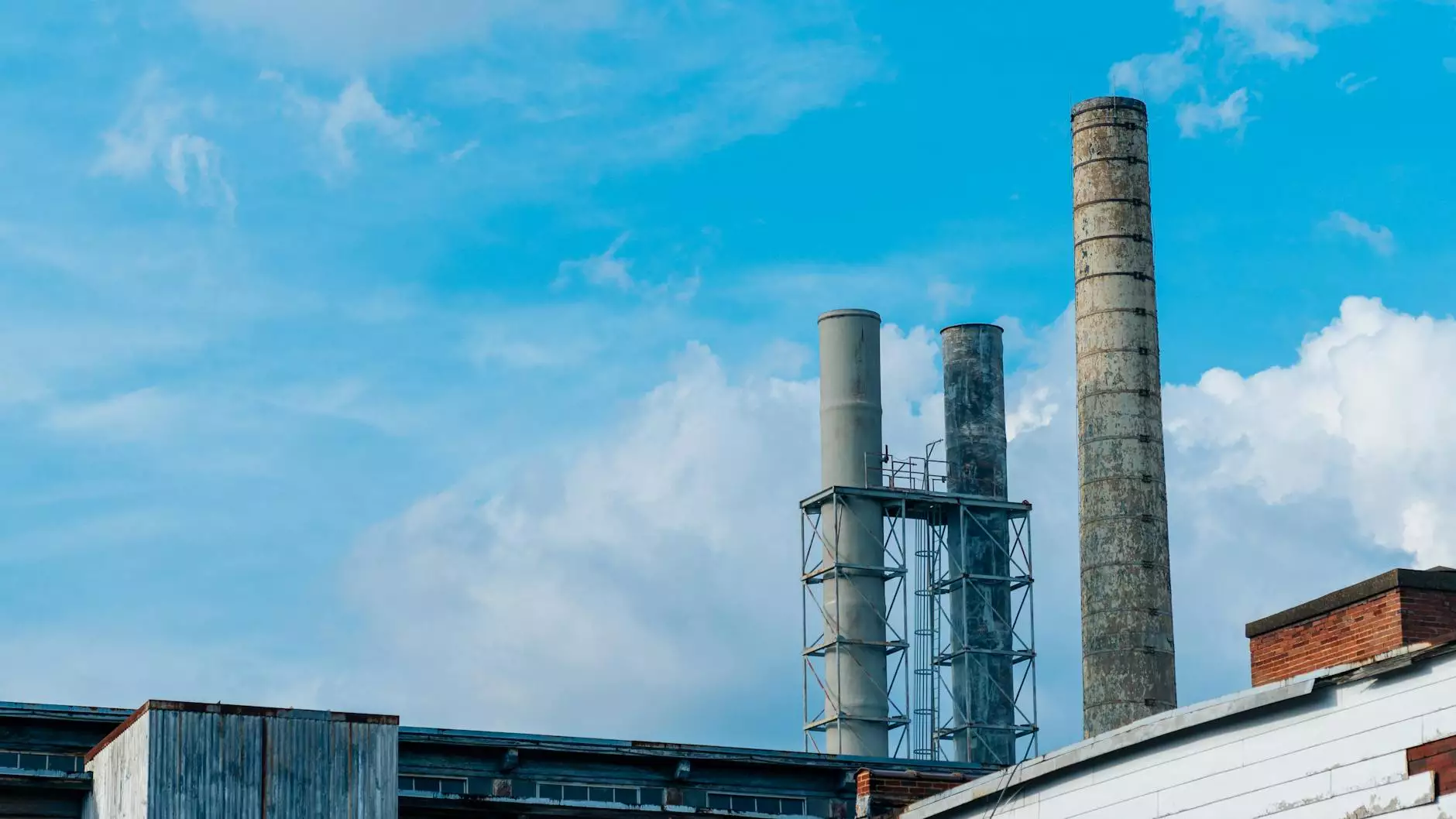
GRP manufacturers play a pivotal role in various industries by producing high-quality, durable, and versatile materials. Glass-Reinforced Plastic (GRP), also known as fiberglass, has become a fundamental component in sectors such as construction, automotive, marine, and even aerospace. This article aims to explore the integral function of GRP manufacturers, their innovative processes, and the benefits that GRP brings to the table.
The Essence of GRP and Its Manufacturing Process
Glass-Reinforced Plastic (GRP) is a composite material made of a polymer matrix reinforced with glass fibers. The resulting material offers high strength-to-weight ratios, excellent corrosion resistance, and exceptional durability. Understanding the manufacturing process of GRP is essential to appreciating why GRP manufacturers are crucial to various industries.
1. The Materials Used in GRP Production
The key components involved in GRP manufacturing include:
- Glass Fibers: These provide tensile strength and help the material resist deformation under stress.
- Polymer Resins: Commonly used resins include polyester, vinyl ester, and epoxy, which act as the matrix ensuring cohesion.
- Additives: Various additives enhance properties such as UV resistance, flame retardance, or improved mechanical performance.
2. The GRP Manufacturing Process
The typical steps involved in the manufacturing of GRP include:
- Preparation: Selecting the appropriate glass fibers and resins based on the desired properties.
- Molding: Using techniques such as hand lay-up, spray-up, or resin transfer molding to shape the resin and fibers.
- Curing: Allowing the composite to harden, often aided by heat, which solidifies the material and enhances its strength.
- Finishing: Trimming, sanding, and applying coatings to achieve the required surface finish.
The Advantages of GRP in Various Industries
GRP’s unique properties offer numerous benefits that have made it a preferred choice among GRP manufacturers. Here are several advantages across different industries:
1. Construction
In the construction industry, GRP is valued for its ability to:
- Provide Lightweight Solutions: GRP components, such as roofing and cladding, reduce the overall weight of structures.
- Enhance Longevity: GRP is resistant to moisture, chemicals, and UV exposure, leading to longer lifespans of building elements.
- Facilitate Design Flexibility: The moldable nature of GRP allows for complex shapes to be created, serving both functional and aesthetic purposes.
2. Automotive
In automotive applications, GRP contributes by:
- Reducing Weight and Improving Fuel Efficiency: Lighter materials lead to better fuel economy.
- Enhancing Safety: GRP parts can absorb impact energy, increasing vehicle safety in collisions.
- Design Versatility: Manufacturers can create intricate designs that are both functional and visually appealing.
3. Marine Industry
The marine sector relies on GRP for:
- Corrosion Resistance: GRP resists saltwater, making it ideal for boats and marine structures.
- Lightweight Construction: GRP enhances speed and efficiency in watercraft due to its light weight.
- Easy Maintenance: GRP surfaces can be cleaned easily and do not require regular repainting like traditional materials.
The Impact of GRP Manufacturers on Sustainability
As industries move towards more sustainable practices, GRP manufacturers are leading the way in developing eco-friendly solutions. The following elements illustrate their commitment to sustainability:
1. Recycling Initiatives
Many GRP manufacturers are pioneering recycling processes that allow for the repurposing of composite materials, reducing landfill waste. Innovations include:
- Upcycling GRP Waste: Transforming discarded GRP into new products.
- Creating Recyclable Products: Developing new formulas that enable end-of-life recycling of GRP components.
2. Energy Efficiency in Production
Enhancements in production processes, like:
- Using Renewable Energy Sources: Many manufacturers are harnessing solar and wind energy to power operations.
- Implementing Energy-Efficient Manufacturing Techniques: This reduces the carbon footprint associated with GRP production.
Challenges Faced by GRP Manufacturers
Despite the benefits, GRP manufacturers also encounter challenges that need addressing:
1. Market Competition
With an increase in demand for alternative materials, GRP manufacturers face stiff competition. To stay ahead, they must:
- Innovate constantly to improve product offerings and reduce costs.
- Expand beyond traditional markets to capture emerging sectors.
2. Environmental Concerns
As sustainability becomes a significant focus, manufacturers must:
- Reduce the environmental impact of raw materials and production methods.
- Adopt eco-friendly practices throughout the production cycle.
Future of GRP Manufacturers
The future for GRP manufacturers looks promising, with trends indicating continual growth and innovation. Key future directions include:
1. Advanced Composite Technologies
Emerging technologies, such as:
- Hybrid Composites: Combining GRP with other materials to enhance properties.
- Smart Materials: Incorporating sensors and systems into the GRP for enhanced functionality.
2. Expansion into New Markets
With the rise of new industries, such as renewable energy (wind turbine blades) and electric vehicles, GRP manufacturers are expected to:
- Invest in research and development to create specialized products tailored to these markets.
- Collaborate with industry leaders to drive innovation and accessibility.
Choosing the Right GRP Manufacturer
For businesses looking to incorporate GRP into their products, selecting the right GRP manufacturer is crucial. Consider these factors:
1. Experience and Expertise
Choose manufacturers with proven track records in the specific applications you require. Experience often translates to quality and reliability.
2. Quality Assurance
Ensure the manufacturer adheres to stringent quality control processes, certifications, and standards to guarantee the durability and safety of GRP products.
3. Innovation and R&D Capabilities
A manufacturer committed to R&D will be in a better position to offer customized solutions and cutting-edge products to meet the evolving market needs.
Conclusion
In conclusion, GRP manufacturers are at the forefront of delivering innovative solutions across a multitude of industries. Their contributions to enhancing performance, durability, and sustainability make them indispensable allies in modern manufacturing. As these manufacturers continue to evolve and adapt, the future of materials science looks bright, promising even greater advancements that will redefine our built environment.
For more information on quality GRP manufacturing services, consider exploring resources like Celtic Composites to discover how they lead in innovation and quality in the industry.