The Impact of Volumetric Concrete Plants on the Construction Industry
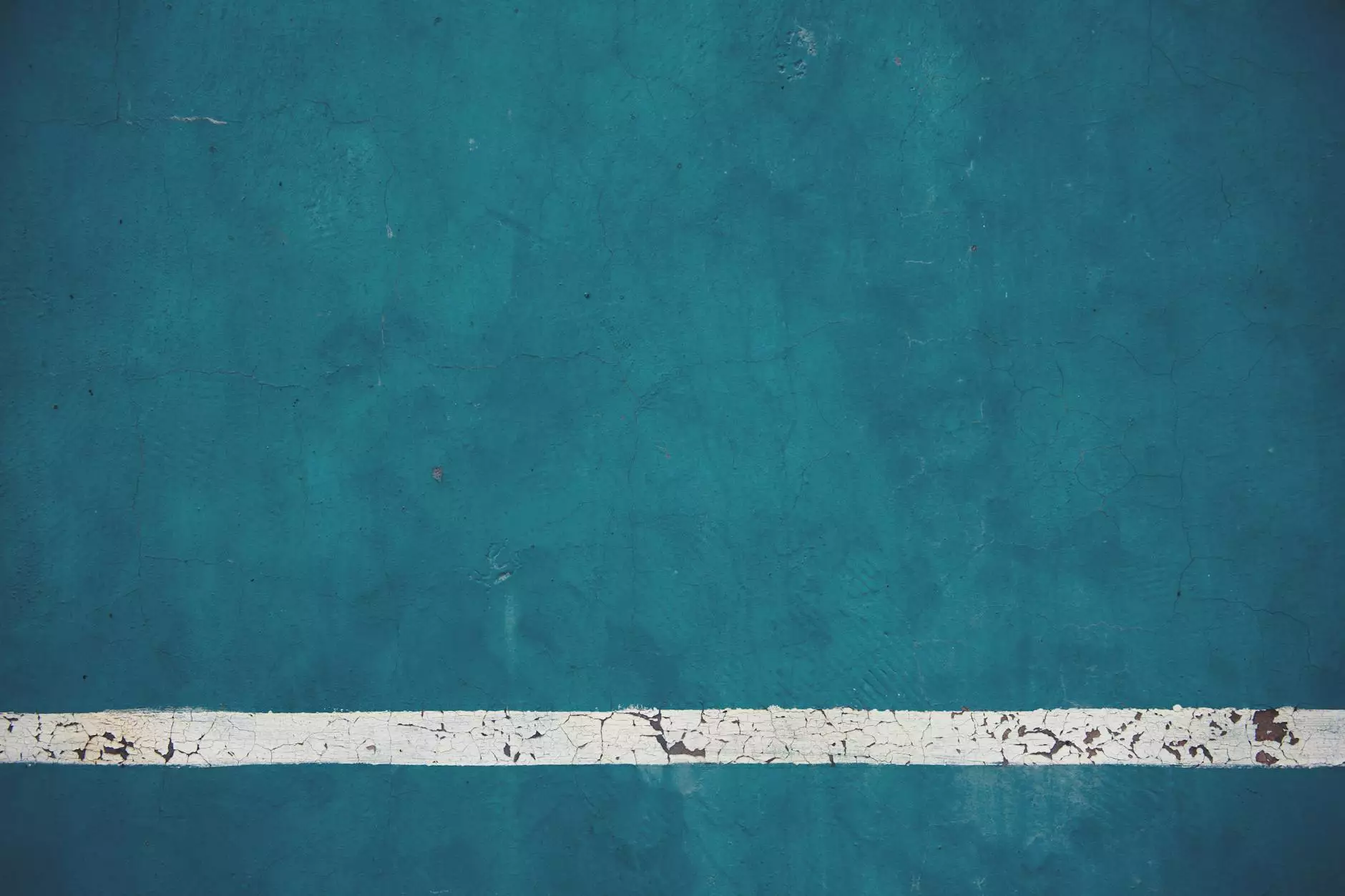
In recent years, the construction industry has seen a significant evolution thanks to advanced technologies and innovative machinery. One of the notable advancements is the volumetric concrete plant, which has revolutionized how concrete is produced and delivered on-site. This article will explore the benefits, functionalities, and applications of volumetric concrete plants, showcasing how they cater to the increasing demands of modern construction projects.
What is a Volumetric Concrete Plant?
A volumetric concrete plant is a specialized type of concrete mixer that enables the on-site mixing of concrete ingredients, including water, cement, aggregates, and admixtures, to produce fresh concrete in the desired quantities and proportions. Unlike traditional batch plants, volumetric mixers allow for the flexibility of producing concrete on demand, ensuring that the right amount is available precisely when needed.
Key Components of a Volumetric Concrete Plant
- Cement Storage: Silos that store bulk cement and facilitate its dispensing during mixing.
- Aggregate Bins: Compartments for storing different types of aggregates, allowing for a variety of mixes.
- Water Tanks: Tanks that hold the precise amount of water required for each batch of concrete.
- Mixing Chamber: The area where all ingredients are combined to create fresh, quality concrete.
- Control Panel: An advanced operating system that allows for meticulous control over the mixing process and proportions.
Advantages of Using Volumetric Concrete Plants
The integration of volumetric concrete plants in construction projects offers numerous benefits:
1. On-Demand Production
One of the most significant advantages of volumetric concrete plants is the ability to produce concrete on-site exactly when needed. This method drastically reduces waiting times and allows for precise control over the quantity produced, minimizing waste.
2. Cost Efficiency
With traditional concrete delivery methods, excess concrete often goes to waste. In contrast, volumetric systems ensure that concrete is mixed per project needs, resulting in significant cost savings. These plants eliminate the risk of over-ordering and reduce transportation costs, making them a smart investment for contractors.
3. Flexibility in Mixing
Volumetric concrete plants offer unmatched flexibility in terms of concrete composition. Operators can adjust the mix design on-site based on the specific requirements of a project, whether it’s for a standard concrete slab or unique architectural applications requiring specialty mixes.
4. Reduced Labor Costs
The automation and efficiency of volumetric mixers often lead to decreased labor requirements. With trained operators managing the mixing process directly through the control panel, the need for additional laborers to handle concrete delivery and supervision is significantly reduced.
5. Enhanced Quality Control
By mixing concrete on-site, contractors maintain better control over the quality of materials being used. This guarantees that the concrete meets the required specifications and standards, reducing the risk of project setbacks due to poor material quality.
Applications of Volumetric Concrete Plants
The versatility of volumetric concrete plants allows them to cater to a wide range of construction applications:
1. Residential Construction
From small-scale home renovations to large residential developments, volumetric concrete plants provide on-site mixing that meets specific residential needs while ensuring consistent quality and cost control.
2. Commercial Projects
For commercial buildings, the demand for quick and efficient concrete delivery is paramount. Volumetric plants help contractors meet tight deadlines while ensuring the availability of concrete in various mix designs, tailored to different structural requirements.
3. Infrastructure Development
Infrastructure projects such as bridges, roads, and tunnels benefit from the flexibility and efficiency of volumetric concrete plants. On-site production avoids delays due to transportation and allows for adjustments in concrete properties to suit environmental conditions.
4. Specialty Applications
Volumetric concrete plants are ideal for specialty applications that demand unique mixes, such as decorative concrete, pervious concrete for drainage, and high-strength concrete for critical structures. They offer the precise customization needed to achieve desired aesthetic and performance outcomes.
Environmental Benefits of Volumetric Concrete Plants
The construction industry has increasingly focused on sustainability and environmental responsibility. Volumetric concrete plants help achieve these goals in several ways:
1. Reduced Carbon Footprint
By producing concrete on-site and minimizing transportation distances, the carbon footprint associated with concrete delivery is significantly reduced. This contributes to a more sustainable construction operation.
2. Waste Minimization
As concrete is mixed to suit specific project requirements, there is minimal waste generated compared to traditional ready-mix operations. The less waste produced means a more sustainable use of resources and materials.
3. Use of Recycled Materials
Volumetric mixing allows the easy incorporation of recycled aggregates and other sustainable materials, promoting eco-friendly practices in concrete production.
Future Trends in Volumetric Concrete Production
The integration of technology in volumetric concrete plants is evolving rapidly, and the future looks promising. Here are some anticipated trends:
1. Smart Technology Integration
With advancements in IoT (Internet of Things) and smart technology, volumeric concrete plants are anticipated to become smarter. Sensors and real-time data analytics will optimize mixing processes, enhance quality control, and improve operational efficiency.
2. Automation and Robotics
Automation will play a crucial role in streamlining operations. Robotic systems may be implemented for material handling and mixing processes, thereby increasing productivity while ensuring safety and reducing labor costs.
3. Enhanced User Interfaces
Future volumetric concrete plants will likely feature more intuitive user interfaces, making it easier for operators to adjust mix designs and monitor production parameters. This will further enhance control and efficiency in concrete mixing.
Conclusion
The advent of volumetric concrete plants marks a pivotal shift in the construction industry's approach to concrete production and delivery. With advantages such as on-demand mixing, cost savings, flexibility, and enhanced quality control, these plants are poised to play a significant role in future construction projects. As technology continues to evolve, we can expect to see even greater efficiencies and capabilities within volumetric concrete systems. Investing in such equipment can significantly benefit construction companies looking to modernize their operations and meet the demands of the ever-evolving market.
Incorporating volumetric concrete plants in projects is not just about keeping pace with current trends but is a strategic move toward a more efficient, cost-effective, and sustainable future in construction.